Sleutelverskil - Perspex vs Polikarbonaat
Ingenieurswese termoplastiese polimere soos poliëtileen, polipropileen, polivinielchloriede, polikarbonaat, poliakrilate is baie gewild in die huidige wêreld as gevolg van hul uitstekende kombinasie van fisiese en chemiese eienskappe. Nie een van hierdie plastiek toon egter volkome volmaaktheid nie. Perspex en polikarbonaat is twee sulke tipes amorfe ingenieurstermoplastiek wat 'n ander stel eienskappe het met hul eie voordele en nadele. Die belangrikste verskil tussen Perspex en polikarbonaat is dat Perspex geproduseer word deur die polimerisasie van monomere van die akrielfamilie, terwyl polikarbonaat geproduseer word deur die polikondensasie polimerisasie van fosgeen en BPA (bisfenol A) of smelttransesterifikasie van DPC en BPA.
Wat is Perspex?
Perspex® is 'n kommersiële naam van akrielplate, wat vir die eerste keer deur ICI-wetenskaplikes in 1934 ontdek is. Perspex® is die geregistreerde handelsmerk van Lucite International, wat onder die Mitsubishi Chemical Corporation bedryf word. Perspex® akriel was die eerste akrielprodukte wat onder sintetiese harse geregistreer is in die vorm van velle, stawe, buise en ander gevormde stukke. Die familie van akrilaat sluit die polimere van die monomere van akrilonitril, hidroksielmetakrilaat, akrilamied, metielsianoakrilaat, etielsianoakrilaat, metielakrilaat, etielakrilaat, trimetielolpropaantriakrilaat en metielmetakrilaat in. Die polimerisasie van metielmetakrilaat in polimetielmetakrilaat (PMMA) was die eerste ontdekking van akrilaatpolimere in 1877 deur die Duitse chemici Fittig en Paul. Na die kommersialisering van akrielplate is dit vir die eerste keer tydens die Tweede Wêreldoorlog gebruik vir windskerms, afdakke en geweertorings op vliegtuie en periskooppoorte op duikbote.
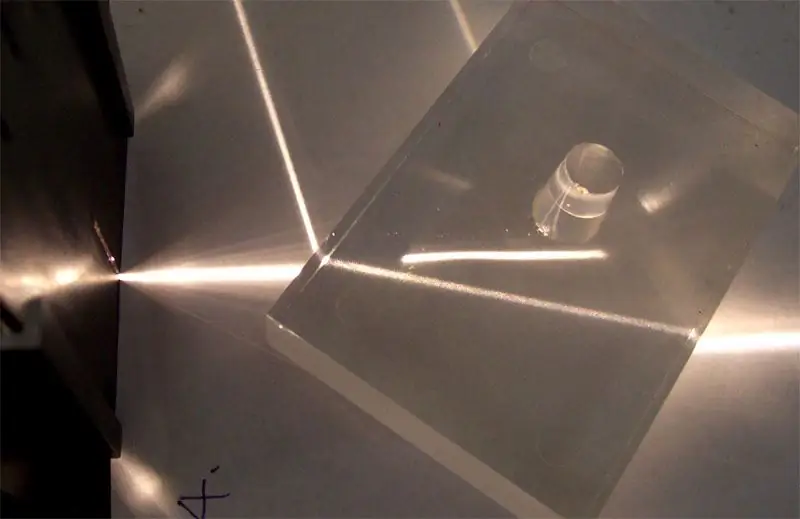
Figuur 1: Breking in 'n Perspex-blok
Perspex® bied uitstekende optiese helderheid, chemiese weerstand, goeie skuurweerstand en uitstekende oppervlakhardheid wat die produk geskik maak vir 'n wye spektrum van toepassings, insluitend optiese lense, mediese diagnostiek, kosmetiese verpakking, en motor-agterligte. Perspex® polimere is ideaal vir ekstrusie en spuitgiet; dit kan gebruik word om beligtingsprodukte soos LED's, geëxtrudeerde diffuserpanele, profiele en buise te vervaardig. In vergelyking met ander kommoditeitstermoplastiek, is akrilaatpolimere duur as gevolg van hul kombinasies van goeie fisiese en meganiese eienskappe soos weerbestandheid, hoë sterkte en briljante helderheid. PMMA het die glasoorgangstemperatuur van 105-107 °C, en die brekingsindeks van 1.49, wat vergelykbaar is met dié van glas (1.60). Daarom word daar soms na PMMA verwys as 'organiese glas.' As gevolg van sy hoë weerstand teen voedsel, vette, olies, nie-oksiderende sure, alkalieë, soute, minerale en alifatiese koolwaterstowwe, word PMMA wyd gebruik as 'n voedselgraad materiaal en as 'n verpakkingsmateriaal. Dit is egter nie bestand teen sterk sure, aromatiese en gechloreerde koolwaterstowwe, ketone, alkohole en esters nie. Die dimensiestabiliteit is goed, maar dit het minder impakweerstand.
Wat is polikarbonaat?
Polikarbonaat is 'n bekende deursigtige en amorfe ingenieurstermoplastiese materiaal wat 'n wye reeks uitstaande eienskappe het. Dit is 'n liggewig termoplast, maar het uitstekende taaiheid, dimensionele stabiliteit, termiese weerstand en optiese helderheid. As gevolg van sy hoë elektriese weerstand, word polikarbonaat wyd gebruik om baie elektriese en elektroniese onderdele en komponente te vervaardig. As gevolg van sy optiese helderheid, word polikarbonaat gebruik om brillense en sekere ander digitale media soos CD's en DVD's te maak. As gevolg van sy wye spektrum van eienskappe, word polikarbonaat in 'n wye reeks toepassings gebruik, van gewone huishoudelike items tot motor- en lugvaarttoerusting en -bykomstighede. Boonop word hierdie termoplastiese materiaal ook gebruik om krapbestande glas, mediese en konstruksietoerusting, onlusteskerms, veiligheidshelms en koplamplense te maak. Die geskiedenis van polikarbonaat gaan terug na die vroeë 1890's, aangesien A. Einhorn die eerste keer polikarbonaatkristalle vervaardig het deur resorsinol en fosgeen in piridienoplosmiddel te laat reageer. Later, in die 1950's, kon kommersiële produsente, naamlik Bayer en GE, die prosesse vir die vervaardiging van polikarbonaathars gebaseer op bisfenol A (BPA) kommersialiseer..
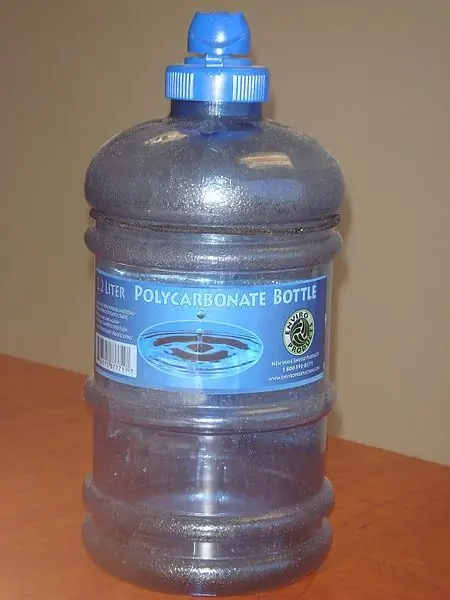
Figuur 2: Waterbottel gemaak van polikarbonaat
Twee metodes word tans gebruik om polikarbonaatharse te vervaardig. Die eerste metode is die twee-fase grensvlak polikondensasie polimerisasie van fosgeen en BPA, en die tweede metode is die smelt transesterifikasie van DPC en BPA by 300 °C en lae druk. Die molekulêre gewig van polikarbonaatharse wissel van 22 000 tot 35 000 g/g mol. Die glasoorgangstemperatuur is tussen 145 - 150 °C. Die teenwoordigheid van lywige aromatiese arielringe in die ruggraat van polikarbonaat is die rede vir sy ingenieurseienskappe. Die smeltpunt van polikarbonaat is ongeveer 230 °C. Dit het goeie dimensionele stabiliteit, kruipweerstand en hoë impaksterkte. Polikarbonaat word as 'n inerte materiaal beskou; daarom is dit wyd gebruik as 'n voedsel-graad plastiek. Die nadele van polikarbonaat sluit in lae UV-weerstand en hidrolise deur alkali-oplossings soos kaliumhidroksied, natriumhidroksied, ens.
Wat is die verskil tussen Perspex en Polikarbonaat?
Perspex vs Polikarbonaat |
|
Perspex is die geregistreerde handelsmerk van Lucite International vir akrielplate. | Polikarbonaat is 'n algemene naam (nie 'n kommersiële naam nie). |
Vervaardiging | |
Perspex word vervaardig deur polimerisasie van akrielmonomere of hul kopolimere. | Polikarbonaat word vervaardig deur intervlak-polikondensasie-polimerisasie van fosgeen en BPA of smelttransesterifikasie van DPC en BPA by 300 °C en lae druk. |
Clarity | |
Helderheid is baie hoog, amper gelyk aan glas. | Duidelikheid is laag in vergelyking met Perspex. |
Glas-oorgangstemperatuur | |
105- 107 °C | 145 - 150 °C |
Weerweerstand | |
Weerweerstand is baie hoog. | Dit het 'n lae UV-weerstand. |
Aansoeke | |
Perspex word gebruik in optiese lense, mediese diagnostiek, kosmetiese verpakking, motor-agterligte, voorruite, ens. | Polikarbonaat word gebruik in krasbestande glas, mediese en konstruksietoerusting, onlusteskerms, veiligheidshelms, ens. |
Opsomming - Perspex vs Polikarbonaat
Perspex is 'n handelsnaam vir akrielplate, wat vervaardig word deur die polimerisasie van akrielmonomere en hul kopolimere. Dit is wyd gebruik in die mediese industrie, lense vervaardiging, motor en verpakking industrie as gevolg van sy goeie chemiese en weer weerstand en uitstekende deursigtigheid. Polikarbonaat is 'n generiese naam vir die industriële plastiek wat uit bisfenol A vervaardig word en het 'n wye reeks toepassings van huishoudelike items tot lugvaart- en motorbedryf. Polikarbonaat is bekend vir sy uitstekende styfheid, lae gewig, helderheid en elektriese isolasie eienskappe. Dit is die verskil tussen perspex en polikarbonaat.
Laai PDF-weergawe van Perspex vs Polycarbonate af
Jy kan die PDF-weergawe van hierdie artikel aflaai en dit vir vanlyn doeleindes gebruik soos per aanhalingsnota. Laai asseblief PDF-weergawe hier af Verskil tussen Perspex en Polikarbonaat