FMEA vs FMECA
Albei, FMEA en FMECA, is twee metodologieë wat in die produksieproses gebruik word, en die basiese feit in die verskil tussen FMEA en FMECA is dat die een die uitbreiding van die ander is. Om verder te verduidelik, is Mislukkingsmodus en -effekte-analise (FMEA) en Mislukkingsmodusse, effekte en kritiek-analise (FMECA) twee tipes tegnieke wat gebruik word om bepaalde foute of foute binne 'n produk of proses te identifiseer en om regstellende stappe te neem om die probleme; en FMECA is 'n ontwikkeling vir FMEA. Hierdie artikel bied aan jou 'n verdere ontleding van die verskil tussen FMEA en FMECA.
Wat is FMEA?
FMEA staan vir Failure Modes and Effects Analysis en dit kan beskou word as 'n stap-vir-stap-benadering om die foute of foute wat in die vervaardigings-, ontwerp- of samestellingsprosesse of binne die produkte of dienste voorkom, te bepaal.
Fuilmodusse beteken die modusse of die maniere wat die mislukkings beïnvloed. Mislukkings kan lei tot klantontevredenheid, wat kan lei tot die vermindering van die verkoopsvolume. Effekte-analise verwys na die bestudering van die gevolge of redes vir daardie mislukkings. Daarom is die doel van die FMEA om nodige aksies/stappe te neem om mislukkings uit te skakel of te verminder, begin met die hoogste prioriteits.
FMEA word tydens die ontwerpstadium gebruik om mislukkings te voorkom. Dan word dit in die beheerstadium gebruik, voor en tydens die voortgesette werking van die proses. FMEA moet in die vroegste konseptuele stadiums van ontwerp begin word en moet regdeur die leeftyd van die produk of diens voortduur.
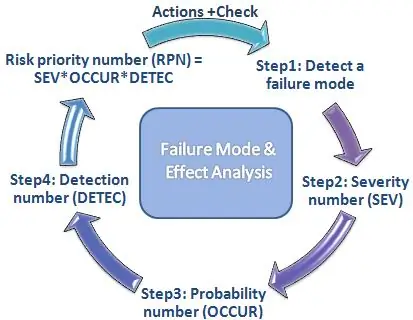
FMEA kan gebruik word in, • Ontwerp of herontwerp van die proses, produk of diens na die geh altefunksie-ontplooiing.
• Wanneer 'n produk met meer kenmerke ontwikkel word.
• Voordat beheerplanne vir 'n nuwe proses ontwikkel word.
• Ten tye van verbetering word doelwitte vir 'n bestaande proses, produk of diens beplan.
• Ontleed mislukkings van 'n bestaande proses, produk of diens.
Wat is FMECA?
FMECA is 'n verbeterde weergawe van FMEA deur 'n kritieke analise-afdeling by te voeg, wat gebruik word om die waarskynlikheid van mislukkingsmodusse te vergelyk met die impak van die gevolge. FMECA kan geïllustreer word as 'n metode wat gebruik word om die foute van die stelsel, die redes agter die mislukkings en die impak van daardie mislukkings te identifiseer. Met die term Kritiek kan die FMECA-proses gebruik word om die areas van ontwerp met groot kommer te identifiseer en daarop te fokus.
Verder kan FMECA nuttig wees om die ontwerpe vir produkte en prosesse te verbeter, wat sal lei tot hoër betroubaarheid, verhoogde veiligheid, beter geh alte, kostevermindering en verhoogde klanttevredenheid. Wanneer die instandhoudingsplanne vir herstelbare stelsels en ander geh alteversekeringsprosedures daargestel en geoptimaliseer word, sal hierdie hulpmiddel nuttig wees.
Daarbenewens word van beide FMEA en FMECA vereis om aan die kwaliteit- en veiligheidsvereistes te voldoen, soos ISO 9001, Six Sigma, Goeie Vervaardigingspraktyke (GMP's), Prosesveiligheidsbestuurwet, ens.
Wat is die verskil tussen FMEA en FMECA?
• FMEA-metode verskaf slegs kwalitatiewe inligting terwyl FMECA kwalitatiewe sowel as kwantitatiewe inligting verskaf, wat die vermoë gee om te meet aangesien dit 'n vlak van kritiek aan mislukkingsmodusse heg.
• FMECA is 'n uitbreiding van FMEA. Daarom, om FMECA uit te voer, word dit vereis om FMEA uit te voer gevolg deur kritiese ontleding.
• FMEA bepaal die mislukkingsmodusse van 'n produk of proses en die uitwerking daarvan, terwyl Kritiekanalise daardie mislukkingsmodusse in volgorde van belangrikheid rangskik deur die mislukkingskoers in ag te neem.